연구실 공용 컴퓨터 모니터가 죽었다. 일부러 그런 것은 아닌데 모니터 목이 부러진 것이다. 때린 것도 아니고 힘을 세게 가한 것도 아닌데 그만 그렇게 되어 버렸다. 황당했지만 당황하지 않고 원인을 살폈다.
다행히 큰 문제는 아닌 것 같았다. 모니터의 목 자체가 부러진 것이 아니라 모니터의 받침대 부분과 화면 부분을 연결하는 부품이 깨진 것이었다. 자세히 보니 나사 구멍은 4개인데 나사는 3개밖에 없는 것으로 보아 이전에 누군가가 손을 댄 것 같다. 나사의 위치도 하중을 받았을 때 부품에 무리가 더 많이 가는 위치로 체결된 상태였다. 그 상태에서 모니터 자체의 무게를 견디지 못하고 나사를 고정시키는 부분이 깨져 발생한 문제였다.
이런 상황들을 종합해 봤을 때, 그냥 깨질 때가 된 것인데 하필 그날 내가 손을 댄 것이라는 것이 내 결론이다. 과정이야 어찌 됐든 내 손을 타서 발생한 일이다. 가능하다면 내 능력 범위 내에서 해결할 생각이었는데 충분할 것 같았다. 단지 플라스틱 재질의 기계적 연결 부품이 깨진 상황에 불과하기 때문이다. 깨진 부품은 다시 만들면 된다. 연구실엔 3D 프린터가 있고 나에겐 기존 부품의 외형과 기능에 맞게 똑같이 설계할 수 있는 능력이 있다.
고려사항
우선 깨진 부품을 다시 보며 3D 프린터로 제작이 가능할지 생각을 해 봤다. 현재 결합을 위한 부품을 만들 수 있는 방법은 시간, 비용을 모두 고려했을 때 결국 3D 프린팅이었기 때문이다.
열
항상 생각하는 열의 관점에서 봤을 때 충분히 가능하다는 생각이 들었다. 모니터 화면도 아니고 뒷부분에서 열이 심하게 발생하지는 않는다. 화면 수준의 발열이 발생한다 하더라도 3D 프린팅에 사용할 PLA 재질을 사용할 때(녹일 때)의 온도가 200°C 부근인 것을 고려하면 전혀 문제가 되지 않을 것이라 생각했다.
공차
실험에 사용한다기보다 일반적으로 컴퓨터를 사용하는 상황에서의 모니터를 생각하면 되기 때문에 흔들림이 많은 상황을 고려할 필요는 없을 것 같다. 컴퓨터를 사용하는 도중에 모니터를 흔들린다는 것은 결국 테이블이 흔들린다는 소리일 텐데 그런 환경에서 컴퓨터를 사용하는 일은 아마 많지 않을 것이다. 그 수준으로 화면이 흔들리면 테이블을 먼저 고정하는 것이 맞다.
그렇다고 화면이 고정되지 않을 정도의 공차는 곤란하다. 지금까지 3D 프린터를 통해 몇몇 부품들을 만들어 본 경험에 기대에 보면 이번 작업은 그리 큰 정밀도를 요구하는 수준은 아니다. 다시 말해 '적당한' 정밀도를 가지면 된다는 것이다. 부품을 체결할 때 나사를 사용하기 때문에 더 그렇다.
강도
모니터 화면의 하중을 지지해야 하기 때문에 충분한 강도가 나와야 한다. 제작한 부품을 통해 모니터를 고정시켰을 때 부품이 깨진다면 모니터 화면이 깨질 수 있고, 이런 상황이 벌어진다면 내 멘탈도 같이 깨질 수 있다.
졸업 작품을 만들 때 3D 프린터로 만든 부품을 많이 사용했는데 이 때 만든 부품은 내가 완성품을 밟고 올라가도 버텨냈다. 경험상 모니터 정도의 무게는 해당 부품으로 충분히 지지할 수 있을 것으로 예상된다. 들어봤을 때 약 2.5kg 정도 되지 않을까 싶은데 그 정도 무게는 충분히 견딜 수 있을 것이다.
아무것도 없는 상태에서 창조하는 것이 아니라 기존의 부품을 더 튼튼하게 만들면 되는 부분이기 때문에 형상은 똑같이 만들고 3D 프린팅 과정에서 밀도를 높이는 등의 방법을 쓰면 모니터 무게를 버틸 수준의 강도는 충분히 가능하다는 것이 내 결론이었다.
제작 과정
앞선 고려사항들은 뭔가 만들 때 매번 고려하는 사항이라 크게 오래 걸리는 과정이 아니었다. 실질적으로 시간이 많이 걸리는 부분은 3D 모델링과 제작이다. 물론 제작은 3D 프린터가 알아서 하기 때문에 내 시간이 소모되지는 않지만 완성품을 보기까지 시간이 오래 걸린다.
3D 모델링
항상 사용하는 오토캐드 프로그램을 사용해 기존 부품을 보고 그대로 따라 만들기 시작했다. 내가 3D 모델링 과정에서 시간이 오래 걸리는 것은 치수 때문이다. 처음 생각한 치수로 모델링을 했을 때 문제가 있을 수 있기 때문에 이런저런 경우의 수를 고려하다 보면 예상보다 시간이 더 걸리곤 한다. 이미 정해진 치수가 있다면 그 시간도 많이 줄일 수 있다. 이번 사례가 그에 해당하는데, 덕분에 뭔가를 처음으로 만들 때보다는 시간이 훨씬 적게 걸렸다.
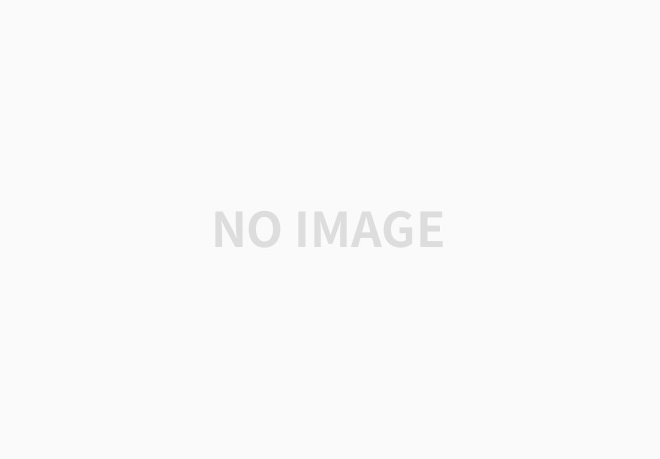
모델링을 할 때는 위의 이미지처럼 항상 다음 단계로 넘어가기 전에 복사본을 만들어둔다. 인벤터나 솔리드웍스같은 3D 전용 모델링 프로그램과 달리 오토캐드는 설계 과정이 따로 저장되지 않는다. (내가 모르는 방법이 있을 수는 있겠다.) 물론 실행 취소를 통해 이전 단계로 돌아갈 수는 있다. 하지만 부품이 완성된 상태에서 수정이 필요한 부분이 초기 단계라면 머리가 좀 복잡해진다. 이런 상황을 직접 경험해 고생한 이후부터는 원하는 단계에서 수정할 수 있도록 일정 수준의 모델링 후 습관적으로 복사본을 만든다.
테스트 진행
부품을 완성본으로 만들어가는 과정에 테스트 단계가 있다. 전에도 언급한 적이 있는데 3D 프린터로 PLA 재질의 부품을 제작할 경우 거의 대부분 수축에 의한 문제가 발생한다. 특히 지금 제작하는 부품과 같이 다른 부품에 나사못 등을 통해 체결되어야 하는 경우 이 차이가 큰 문제가 될 수 있다. 따라서 실제로 측정한 치수를 그대로 제작 단계에 적용하는 경우는 거의 없다. 최종 결과물에서 문제가 생길 수 있다. 이를 방지하기 위해 중간중간 테스트 단계를 거친다. 예를 들면 제작하는 부품에서 다른 부품과 연결되는 부분만 먼저 프린팅 해보는 것이다.
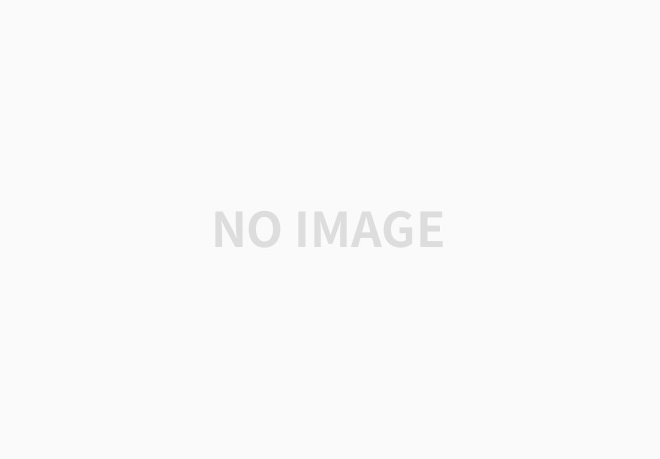
위 이미지처럼 체결될 부분에 대해 먼저 프린팅을 진행했다. 구멍이나 요철은 분명 결합할 부품과 맞아떨어져야 하기 때문에 매우 중요하다. 3D 프린팅을 통해 (내 생각에는) 제법 많은 부품들을 만들어 왔는데 수축에 의한 공차를 예측하는 것은 아직도 어렵다. 대략적인 경향성을 알고 있기 때문에 테스트 수가 보통 3번을 넘지는 않지만 그래도 한 번에 맞추는 경우는 드물다.
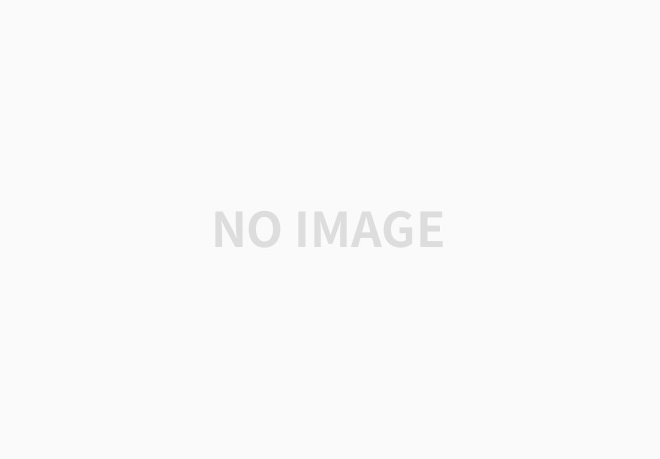
테스트 단계를 거쳐 프린팅을 했을 때 기존 부품과 실제로도 똑같은 크기가 나오도록 모델링을 완성했다. 이 파일을 stl 파일로 저장한 뒤 슬라이서 프로그램을 사용해 G-code로 변환하고 3D 프린터로 출력하면 된다.
적층 방향
모델링과 테스트가 끝난 뒤 전체 제품을 프린팅 한다. 이때 적층 방향을 고민하는 편이다. 사용할 3D 프린터가 FFF (Fused Filament Fabrication) 혹은 FDM(Fused Deposition Method) 방식이므로 녹은 필라멘트가 노즐의 움직임에 따라 원하는 형태의 단면을 쌓아 올리는 과정을 통해 형상이 만들어진다. 따라서 자연스럽게 결이 발생하기 마련이다. 경험상 단지 고정을 위한 부품에서 이 부분에 대한 영향은 거의 없는 수준이지만 습관적으로 항상 고민하게 된다. 평소에는 보통 부품의 강도보다 외적인 형태 때문에 적층 방향을 고려하는 편이다.
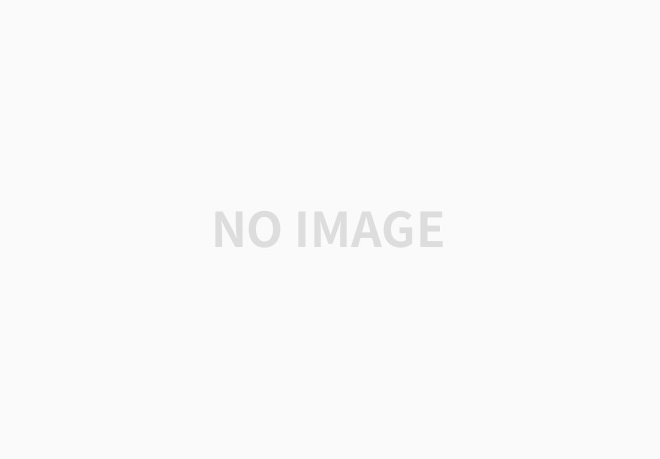
3D 프린팅 결과물의 적층 방향에 따라 다르게 작용하는 외부 힘(F)을 위의 이미지와 같이 표현할 수 있다. 아마 왼쪽 그림이 더 안 부러질 것 같다는 느낌을 받을 수 있을 것이다. (이는 normal stress와 shear stress의 차이에서...) 실제로도 그렇다. 따라서 부품을 설계했을 때 힘을 많이 받는 부분이 이미지의 왼쪽과 같은 상황이 되도록 프린팅 방향을 조절한다.
후처리
이번에 만든 부품은 형상이 제법 복잡한 편에 속한다. 여기서 복잡하다는 것은 서포트가 필수적으로 필요한 부분이 있다는 뜻으로 썼다. 다시 말해, 적층 방향을 고려해 어떤 방향으로 두고 프린팅을 해도 역구배(허공에 떠 있는) 형상이 발생할 수밖에 없다는 뜻이다.
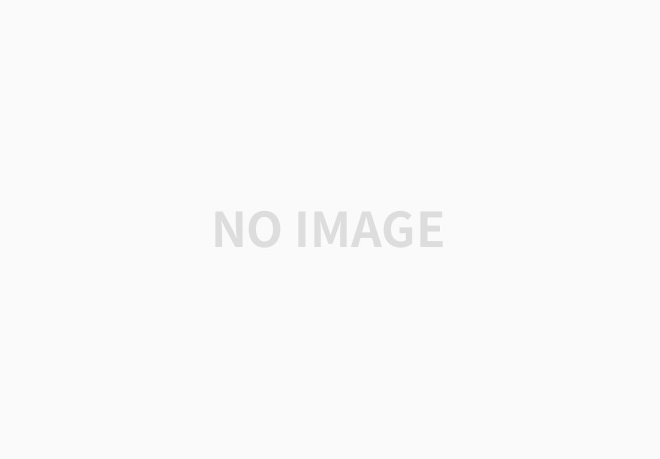
3D 프린터가 stl 파일을 G-code로 변환하는 과정(이 과정은 이전 글에서 설명한 적이 있다)에서 위의 이미지와 같이 비어 있는 중심 부분에 서포트가 자동으로 생성된다. 허공에 해당하는 부분의 면적이 좁으면 품질을 포기하고 프린팅이 가능하긴 하지만 이번 경우는 넓은 편에 속하기 때문에 어쩔 수 없이 서포트를 사용해야 했다. 부품과 같은 재질을 사용하면 서포트가 받치는 아랫면의 품질이 좋지 않고 서포트를 제거하기도 힘들다. 따라서 새로운 재질을 서포트로 사용하기로 했다. 바로 PVA+ 재질이다.
PLA 재질은 물에 녹지 않지만 PVA+ 재질은 물에 녹는 재질이다. 다시 말해 PVA+ 재질을 사용해 서포트만 선택적으로 제작하게 되면 완성품을 물에 넣어 서포트를 깔끔하게 제거할 수 있다는 뜻이다. 덕분에 부품에 가해질 힘만 고려해서 프린팅을 진행할 수 있었다. 위와 같은 제작 공정이 가능한 이유는 연구실에 있는 신도리코사의 3DWOX 2X가 노즐이 두 개이기 때문이다. 덕분에 두 개의 다른 재료를 동시에 프린팅 할 수 있다.
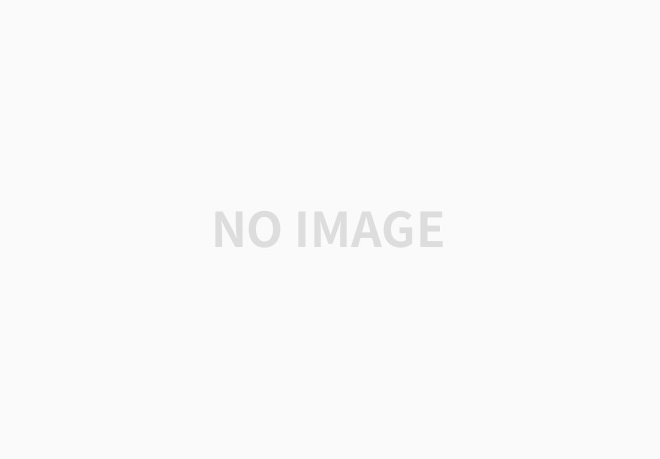
위 이미지에서 볼 수 있듯, 프린팅을 완료하면 왼쪽 이미지와 같은 결과물이 나온다. 이를 뒤집어보면 부품의 비어있는 아랫부분은 오른쪽 이미지와 같이 흰색 PVA+ 재질로 채워진다. 부품을 실제로 사용하기 위해 하얀 부분(PVA+)을 제거해야 한다.
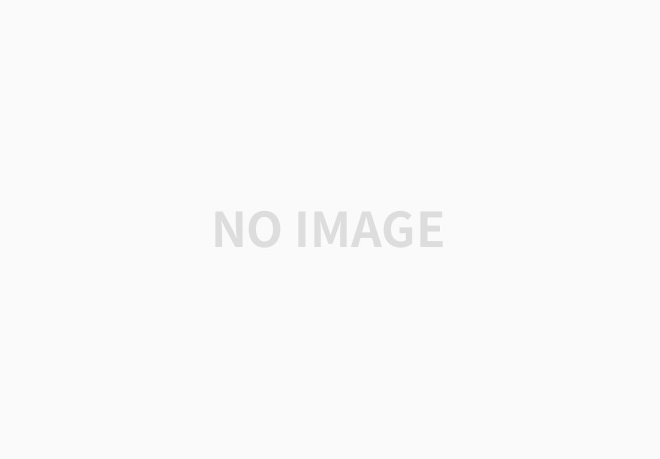
서포트에 사용된 PVA+ 재질은 앞서 언급했듯 물에 녹는 성질이 있기 때문에 제거하는 것이 크게 어렵지 않다. 위의 이미지와 같이 단순이 물에 담그면 그만이다. 저 사진은 그냥 차가운 수돗물을 사용한 모습이다. 따뜻한 물을 사용하면 더 빨리 녹일 수 있지만 굳이 그럴 정성은 없었다. 덕분에 제법 시간이 걸렸던 것 같다. 중간중간 물을 갈아주는 과정이 있었다.
이 과정에서 PLA 재질의 부품 틈새로 물이 스며들었다. 프린팅 시간이 오래 걸리는 문제도 있고 굳이 그렇게까지 할 필요가 없어 내부 밀도를 100%로 설정하지 않았기 때문일 것이다. 아마 밀도를 100%로 설정했어도 물이 스며드는 문제는 발생하지 않았을까 하는 생각이 들긴 한다. 가만히 두면 마르겠지만 더 하루라도 빨리 모니터 수리를 완료하고 싶었기 때문에 그냥 진공펌프를 사용했다. 펌프를 작동시키자 압력이 낮은 부품 표면으로 물이 스며 나왔다. 휴지를 함께 넣어 진공펌프가 꺼졌을 때 물이 다시 부품 내부로 들어가는 상황을 방지했다.
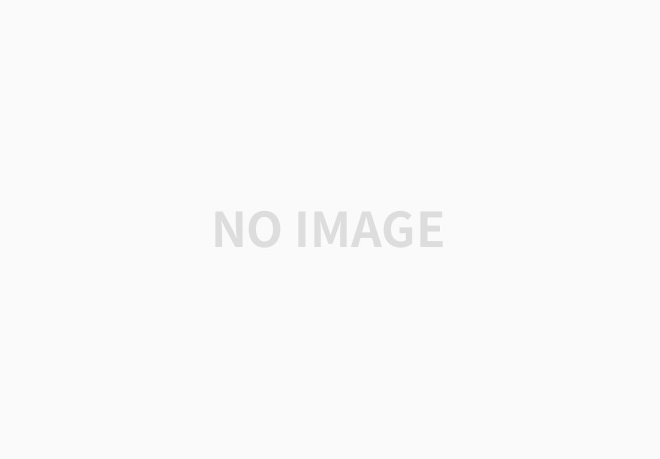
위 이미지는 앞선 과정을 모두 거쳐 PVA+ 재질을 모두 제거한 모습이다. 이제 조립해서 제 기능을 하는지 확인하는 일만 남았다. 제대로 만들었기 때문에 별다른 문제없이 잘 조립될 것이라 확신하고 있었다.
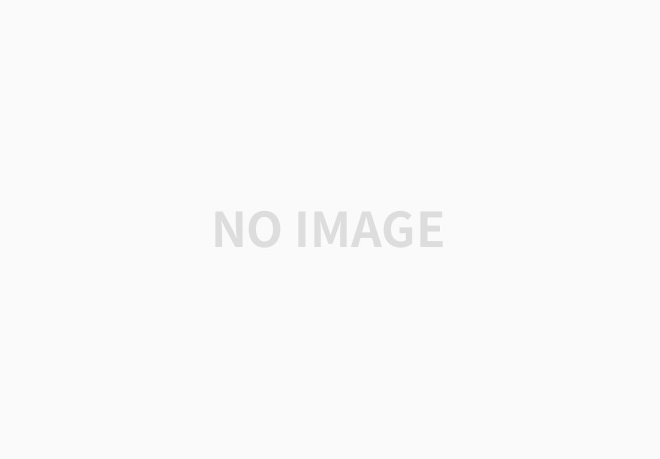
확신한 대로 부품은 필요한 자리에 딱 들어맞았다. 테스트까지 진행하고 만들었으니 당연한 결과였지만 만든 부품이 이렇게 딱 들어맞을 때마다 느껴지는 뿌듯함과 만족감은 항상 새롭다.
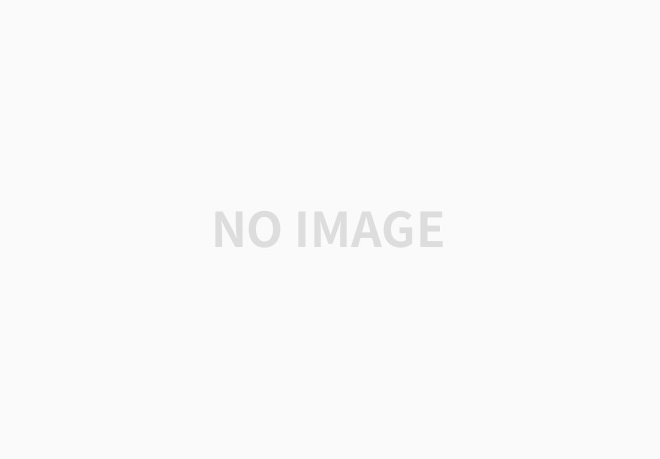
기존에 있는 부품을 만드는 것이 필요한 부품을 직접 만드는 과정보다는 확실히 쉬운 것 같다. 무사히 원래 모습으로 돌려놨으니 하는 말이지만 모니터가 덜컹했을 때 심장도 같이 덜컹했었다. 차분하게 생각해보니 만들 수 있을 것 같아 시도했는데 아직까지 멀쩡하게 잘 사용하고 있다. 다행히 내가 엎지른 물은 다시 주워 담을 수 있었던 것 같다.
'만드는 공대생 이야기' 카테고리의 다른 글
만들기 : 3D 프린팅을 통한 우산 손잡이 제작 (0) | 2020.08.22 |
---|---|
만들기 : 3D 프린팅을 통한 버킷(bucket) 거치대 만들기 (feat. 초원심분리기) (0) | 2020.07.18 |
만들기 : 3D 프린팅을 통한 카메라 거치대 업그레이드 (0) | 2020.05.14 |
만들기 : 무소음 마우스 개조 (6) | 2020.03.22 |
만들기 : 3D 프린팅을 통한 컵 홀더 제작 (0) | 2020.02.24 |
최근댓글